Printed circuit boards are the backbone of any electrical and electronic device. The functioning of the device depends on the PCBs and it plays an important role in the reliability of a product. At the same time, OEMs and enterprises seek more robust design, reduced life cycle costs and reliable products to market in a short time. Thus, testing and verification of products play a crucial role at every stage of the product life cycle in terms of design, circuit, functionality and so on.
In this blog, we stress on two types of tests – HALT Testing and HASS Testing. HALT and HASS testing allow manufacturers the opportunity to remain competitive by offering test recommendations in the design phase or prior to the manufacturing release.
What is HALT Testing and HASS Testing?
HALT (Highly Accelerated Life-cycle Test) is a kind of stress testing to validate product reliability during the engineering development process and HASS (highly accelerated stress screening) is majorly used during mass production to screen-out weak PCBAs. Both are commonly applied to electronic equipment and are performed to identify/resolve design weaknesses in newly-developed products.
During the HALT Testing, incremental step stresses (Temperature, Vibration and Combined Temperature and Vibration) are applied until the product fails. Hence, HALT supports to determine product’s weaknesses, operational design margins and destruct limits during PDLC & HASS support for screening before field deployments. HALT is generally performed on MVP (Minimal Viable Product) Prototype DUT (Device Under Test) during the design phase of PDLC while HASS is useful for mass production cycles to identify manufacturing flaws (if any) within a very short time period.
HALT is important to precipitate integrated product’s latent failures at component-level which might be caused by process or design weaknesses. So, it is necessary to stress-out a product beyond desired/expected field environmental conditions and each stress should be applied in a stepwise manner – like thermal and vibration stresses incrementally. Sometimes, input and output (AC/DC Voltage Variation) loading stresses can also be applied to make it more effective, majorly applicable to PSU (Power Supply Units).
Why is the HALT/HASS Test Chamber Important?
Unlike other environmental simulation chambers, HALT and HASS chambers offer fast temperature ramp rates (up to 60C per minute) and combine thermal, vibration, and shock simulation in a single apparatus. Vibration levels up to 50 Grms can be applied simultaneously in three linear axes (X, Y, and Z) and three rotational axes (pitch, roll, yaw).
How Does HALT Enhance the Robustness of the Product?
HALT testing is basically used to incrementally apply high-stress levels for short time durations which is known to be beyond the expected field environment scenarios. The benefit of using an incremental step stress approach is to deliberately stretch all variables until any anomalies occur. As HALT testing is purely designed to precipitate failures, it is not just like a pass/fail test but surely requires RCA (root cause analysis) on certain failures and corrective measures to achieve optimum value from overall testing. It flourishes our ability to learn & scrutinize more about the product’s design and material limitations. However, it provides several opportunities to continuously improve the design in the Development/Prototype stage before the market launch.
A complete HALT testing includes five different individual profiles to Test
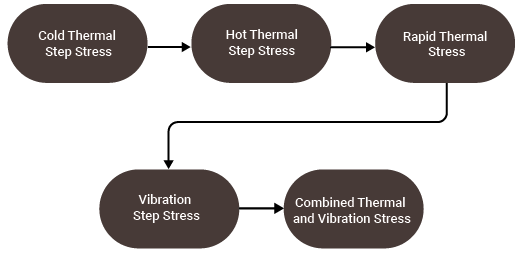
- Low/Cold Temperature Step Stress
- To expose the product in decreasing temperature by ~10°C steps for dwell-time of ~10-15 minutes at each step this cycle repeats until the product begins to perform abnormally. Record its first abnormality labeled as LOL(Lower operating limit) to take corrective action for further analysis. Still to decrease stress until the product returns to normal operation after reducing the stress, record it as LDL(Lower Destruct Limit) for further analysis.
- High/Hot Temperature Step Stress
- To expose the product in increasing temperature by ~10°C steps for dwell-time of ~10-15 minutes at each step this cycle repeats until the product begins to perform abnormally. Record its first abnormality labeled as UOL(Upper operating limit) to take corrective action for further analysis. Still to increase stress until the product returns to normal operation after reducing the stress, record it as UDL(Upper Destruct Limit) for further analysis.
- Rapid Thermal Cycling
- Further in temperature evaluation, rapid thermal stress is applied to the product based on thermal operational limits found during step stressing. The ramp rate temperature change is set to maximum possible value dwelled for ~10 minutes to achieve thermal stabilization while executing test diagnostics. At least five such thermal transition cycles are applied to uncover any weaknesses related to thermal rate/range. Lastly, return the HALT chamber to 20°C (room temperature) & retest to verify no product performance degradation.
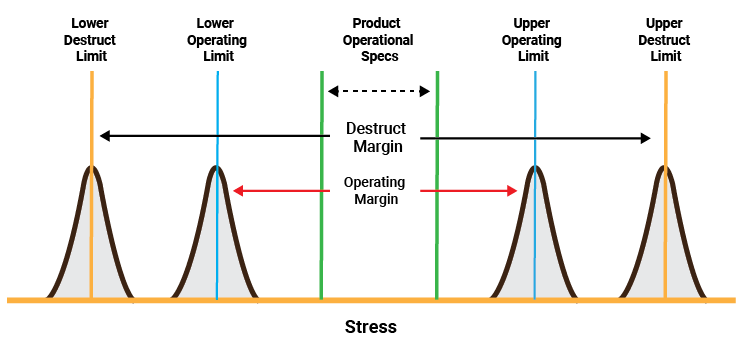
- Vibration Step Stress
- To stress with Vibration parameter, Vibration Step Stress is useful once product is securely fastened to a vibration table using some-kind of mechanical fixture (to simulate same as the actual mounting/orientation/installed position/condition) at temperature set to 20°C (room temperature). To start with 5/10 Grms vibration level & increase it by 5/10 Grms (dwelled for ~10 minutes to run diagnostics) depending on product specifications & continue this process until UOL and UDL of vibration are obtained. Then, reduce stress to ambient normal conditions to take corrective action.
- Combined Environment
- Combined stress is the final step in the HALT test process. Considering all previously applied stresses, the same rapid thermal transition profile is used. For vibration, each step will be equal to step-stress DL divided by five. Dwell time at each temperature limit is to set ~10 minutes & vibration to be constant for each rapid thermal transition cycle. Such five cycles of combined rapid thermal & vibration steps are useful for uncovering the additional defects.
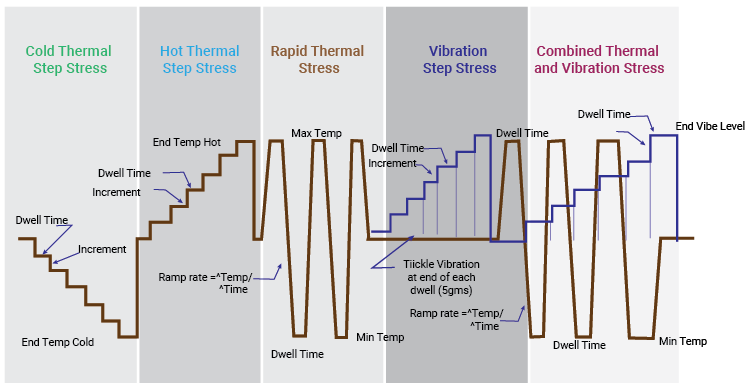
Each of the above tests are conducted with a specific goal (i.e. examining material degradation in cold and hot environments, discovering mechanical issues & to better understand the potential electrical & mechanical issues against the desired performance).
However, power on/off cycling may not be appropriate for every product, sometimes it is applied at every temperature or vibration step to induce additional electrical stresses simultaneously. Such power cycles should be conducted quickly but with sufficient allowed time to generate any artificial excessive overloads & failure modes.
When a failure occurs during an ongoing Test Cycle/Profile, Test is immediately stopped to record/document failure’s stress level. After implementing a temporary “fix” it is tested continuously at higher levels of stress. This would be helpful to precipitate any type of latent & inherent defects in design, component level, or in manufacturing process. To accelerate parallel testing, typically 1 to 4 DUTs can be used simultaneously (if possible & practical enough considering DUT/Setup cost and size of the product). Also, few spare parts OR backup units (not under test) would be required to repair quickly as “temporary fix” to continue with testing soon unless non-repairable failure occurs.
HALT Test is considered as SUCCESS only when failures are produced, corrective action implementation after RCA to define actual expanded product limits. HALT readings & results are used to develop/finalize a HASS screening profile as a POST-Production process. HALT is not a Pass/Fail test, but helps to identify the weakest points in the design of a product and thus helps the product design to be improved to increase the reliability/life of the product.
Below is a distribution of type of failures generally observed in typical products:
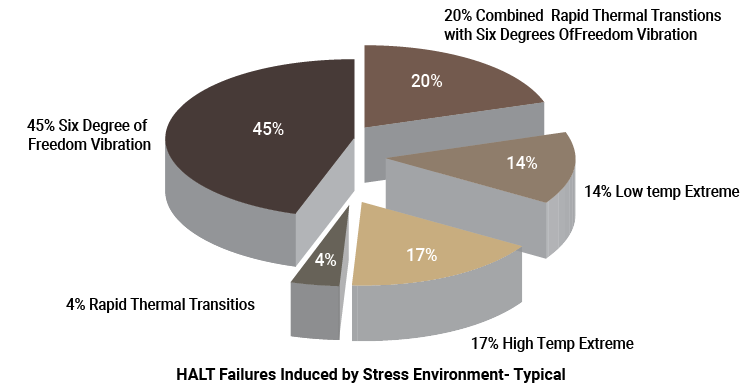
- HALT validation lowers product development costs significantly
- Prevents costly re-design or amendment in product development cycle
- Better product to market/sale with robust design, higher reliability and quality assurance
- Improves time-to-market by reducing overall product development time
- Enable discovery of any physical limitations of a design
- Better accuracy in forecasting product life expectancy with mean time between failures
- Reduced manufacturing screening costs & overall reduction in warranty claim costs
- Early information to predict production maturity (with stabilized yields per batch)
How does HASS help in the Screening Production Process?
HASS stress levels are typically less compared to HALT, because the goal is to expose 100% units (or samples) at max reasonable stress to find faults – but not to reduce product’s life. HASS is a kind of PASS/FAIL testing, & its profile should be finalized after POS (Proof-of-screen) process – a process ensuring that a screening would not damage working hardware and sufficiently effective to detect defects in a product. In POS, it’s suggested to run the desired HASS process ~15 to 30 times to ascertain that the screening profile is not removing excessive life from the product. HASS test helps in rejecting the samples with early failures in the production batches.
Benefits of Product Testing Through HASS Testing
- Helps in hidden or latent failures precipitation induced by either poor labor or manufacturing processes
- Also detects infant mortality of weak components to weed-out faulty assembled PCBs
- It verifies integrity of mechanical assembly
- It helps in filtering out flawed units before reaching to end-user/customer
- Decreases warranty and RMA/field service costs
- Uncovers integrated problems caused by changes of Hardware, Firmware & variations in manufacturing
- Unveils BOM component supplier quality issues and any part revision changes
VOLANSYS has proven expertise in hardware engineering services & solutions and has helped one of the clients by developing an IoT gateway targeted for telematics & fleet management applications. Such Gateways are generally installed on mobile fleet vehicles (e.g. heavy/light/medium duty trucks), so our quality engineering team opted for HALT testing to vary Temperature & Vibration parameters to simulate against actual environment operating conditions. The team referred to SAE-J1455 automotive standard documents to derive & execute HALT test specifications. Based on HALT results, they deployed a simple HASS screening (1 Hour at 60C) for the mass production process as well. Overall, HALT & HASS ensures reliability & quality of all PCBA components to offer ~3 years of Product warranty. Read more about our hardware engineering services success stories.
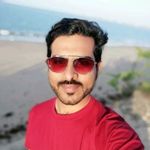
About the Author: Jay Patel
Jay Patel is associated with VOLANSYS Technologies as Principal Engineer for more than 4 years. He has rich experience working in Embedded Hardware domain involving product design right from concept/feasibility, system architecture, PoC/MVP, final product certification to mass production transfers. He also supports field trials/deployments of consumer and industrial products for our clients.