The journey from idea to market-ready product becomes significantly faster with the tightly integrated product engineering lifecycle for manufacturing. However, to meet the product requirements and make it easily manufacturable, running through each stage of the product life cycle from concept to manufacturing and exploring the specific considerations is important.
The aim is to support OEMs and enterprises that are embarking on IoT product development to be able to accelerate their speed to market as a result of following the steps outlined here.
Each Stage Key Elements in Product Design Lifecycle
- Product Concept, Feasibility and Architecture Finalization
At this stage the aim is to clearly identify the new product, based upon the organization’s strategy, marketing objective and customer demand. Generate and resolve queries to make the requirements more clear.
- In-depth requirements understanding – The basic idea of the product should be formatted as a document to map with the traceability matrix during product manufacturing transfer
- Feasibility study and analysis – It is important to identify unknown sections and validate with hardware and software simulators. Also, check the functional behavior with different analysis tools like Multisim, Proteus, LTspice, etc. to reduce time and cost of the design
- Selection of hardware and software platforms – There is no “one-size-fits-all” approach to select hardware and software for developing IoT solutions. For example, adopting standard-based hardware like microcontrollers can save time and expense in the early stages of development without sacrificing flexibility. However, one should choose such that both are compatible, integrable, portable, modular, have sufficient capacity, cost-efficient, risk-free, optimized, easy to use, high performance, power-efficient, secure and bug-free
- DFM, DFA and DFT aspects during the concept phase – It is one of the most important technical aspects to freeze the components, behavior, design flow and finalize architecture to make it easily manufacturable, assembled and tested based on the suggestions and guidelines
- Product Design & Development
Indeed, nearly 80% of the cost of the manufactured product is determined by decisions made during the design and development processes and this decision-making often occurs during the first 20% of the design process in electronics manufacturing services. Thus, it is important to consider manufacturability in the early stage for product quality, reliability, testability, serviceability and customer values.
- Simulation – The hardware, firmware and mechanical simulators are the key elements to derive the system function based on the raw performance, timing accuracy and modeling
- Modular hardware, software co-design approach – This is one the best techniques to optimize the complex product and constraints such as power, performance, and cost
- Design verification and code validation at each stage – This approach will reduce the risk of design and help create the right product to meet the time to market. We at VOLANSYS, follow the schematic, layout, Gerber, mechanical CAD checklist tools to validate design and code to avoid mistakes during the design stage
- BOM review and optimization – It is very important to estimate the product cost of manufacturing during the design stage to avoid iteration, additional cost and time. This stage is generally taken care of as a part of the DFMA process we follow at VOLANSYS
- Review DFM, DFA and DFT aspects during design – The design approach is followed with specific guidelines and suggestions to meet the user expectations. The DFM covers verification of PADs and drilling optimization, stack-up details, fabrication material and tolerance, BOM alternates and optimization, parts evaluation, assessment and design review
The DFA covers parts placement feasibility, assembly checklist, easy electromechanical fitment, IPC-based stencil requirements, smooth surface mount technology pick and place process, thermal profile selection, through holes guide and assemblyThe DFT covers test plans including EDVT, test points and breakpoints, test coverage, semi or full automation tools like python scripts, QT based-GUI, test Fixture requirements, etc. - Mechanical aspects during design – Avoid or shorter overhangs and undercuts in parts design, draft corners in vertical surfaces of parts, minimum radius in internal corners, edges, achievable tolerance, deformations and internal stress, requirements of Test Jig fixture, Surface finishes like painting, texture, polish, etc.
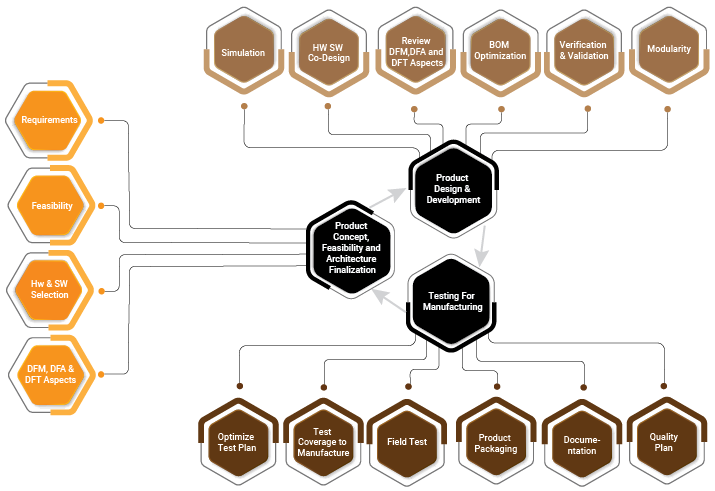
- Product Testing
Testing during production normally has three overall goals: to carry out a functional test, product hardware and firmware bring-up tests and certification tests. Functional testing is intended to cover all the functional requirements with specific test ID to map with the acceptance criteria and to verify that each instance of the product works as designed.
Product hardware and firmware bring-up tests planned with specific critical test points and breakpoints aims to validate the platform. After validating these tests, plan multiple trials at actual fields. This results in optimized design with a good quality product. At the same time, conduct certification to eliminate the electromagnetic compatibility (EMC) and electromagnetic interference (EMI), environment and reliability related defects from the design and make it optimized to comply with the product.
- Evaluate/Optimize Product Functional Test Plan vs. Requirements vs. Execution – It should cover optimized in-depth test planning and execution of hardware tests such as visual tests, impedance tests, power tests, functional tests, EDVT and certification tests. The firmware tests cover the interface tests, memory stress tests, SDK level tests, library level tests to validate the overall application
- Plan, evaluate and resolve field test results – In this stage, use different tools, accessories and cloud platforms to track the product functionality with a specific timeline to derive the actual behavior
- Refer and evaluate compliance test plan requirements – The product should not harm by or from the environment. To achieve that, IoT service providers must use the spectrum analyzer, vector network analyzer, thermal chamber, Line Impedance Stabilization Network, different RF antennas and other RF cables and accessories
- Evaluate documentation package – The documentation package includes the latest revision of the item code, hardware and mechanical BOM, optimized test procedure, test Jig/setup details, PCBA test report, assembly instructions, debugging and repairing guide, harness test plan & procedure, programming instructions, IQC reports, previous proto batch learning in documents and PCBA labeling information & guidelines
- Evaluate and optimize testing coverage – It is a part of DFT to measure the test quality based on the diagnosis of the critical components. The flying probes techniques and reliability tests will help to identify the critical section and diagnosis to optimize the coverage
- Evaluate quality plan – This is an important stage for cross verification of the product to validate it with a different process-oriented plan which covers certifications, reliability tests, FMEA, yield, etc.
- Good product labeling and packaging – The product should have minimum user instruction documents and have a small but effective packaging and labeling plan. The label should be short and simple and cover all the product identification details
Read our success stories to know how VOLANSYS experienced team in hardware engineering services, mechanical design engineering services and embedded engineering services helps organizations design and develop manufacturing ready products for their businesses.
Whether you are in manufacturing, healthcare, consumer electronics, retail, automotive or any other industry, your operations and IT teams will have a list of problems and opportunities to address to improve business processes. Selecting the right IoT solution provider will help develop manufacturing-ready products to address your pain points and business objectives.
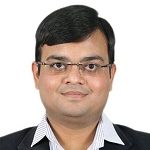
About the Author: Nilav Choksi
Nilav Choksi is working with VOLANSYS Technologies as Tech Lead under PES Hardware design domain. He has a total 9 years of diversified experience in the field of Embedded Hardware board design, Wireless domain for consumer, Aerospace and industrial Electronics. He has end-to-end product development experience, starting from customer requirements to design, development, and hardware bring-up to implementation to product certification to Manufacturing.